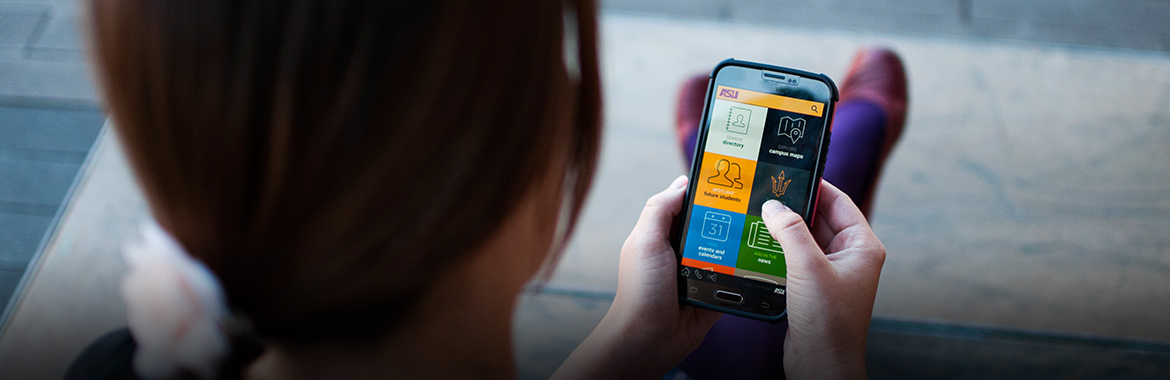
In The News
Lean Six Sigma Green Belts Finding Success with Foundational Tools
For several years, the office of Global Outreach and Extended Education at Arizona State University has offered a portfolio of Lean and Six Sigma professional certifications. Led by engaged and highly experienced Lean and Six Sigma practitioners, these programs offer a wealth of knowledge and tools to be implemented by professionals in their careers and beyond.
One of these talented practitioners is Clayton Taylor, Director of Organizational Performance for Arizona State University’s Business and Finance Support Services. A Six Sigma Master Black Belt himself, Clayton is responsible for the instruction of a portfolio of professional programs and plays a pivotal role in the partnership between the Office of Business and Finance and Global Outreach and Extended Education.
With his unmatched level of knowledge and understanding in Lean and Six Sigma, we invited Clayton to provide his perspective, experience and recommendations in a question-and-answer format. and encouragement to organizations and individuals alike to invest in the use and application of Lean Six Sigma tools for the increased positive impact on organizations and their customers.
What could cause hesitation for those interested in participating in a lean six sigma program?
In some ways, Lean Six Sigma can be daunting to people who are unfamiliar with these methods. These methods are known for having extensive toolsets and a reliance on statistics and other mathematics to aid in understanding processes and making decisions.
I can remember a time when practitioners used to boast about the tools they used, making it seem to others as though Lean Six Sigma practitioners were an elite group. These misperceptions can lead individuals and ultimately organizations to shy away from using these methods because they feel that they are too complex, only usable in manufacturing environments or by industrial engineers.
The reality of Lean Six Sigma is that it contains a core of simple, yet powerful tools that can be learned and used by anyone, at any skill level, to make breakthrough improvements in their processes, regardless of the industry in which it is applied.
What are some of the tools participants learn in a lean six sigma program that can be immediately applied to their job?
Tools like process mapping, Pareto analysis, histograms, fishbone diagrams, 5 whys, and control charts, are easy to learn and can lead to great process improvements.
One of the key things that we strive to do in our training programs is to make the material accessible to everyone. We show how Lean Six Sigma can be applied to any process in any industry. We do not aim to make people mathematicians, but instead show them how to use statistics in their assessments, how to select the right tools to understand processes, and how to make use of software to get the answers they need to make decisions.
We see this happen time and again in the projects that are completed by Green Belt students as a requirement for the completion of their professional certifications. The projects provide the students an opportunity to practice and demonstrate the application of what they’ve learned. The projects also allow the students to explore the tool sets and ultimately make a meaningful impact on their organizations.
As an instructor, could you provide examples of previous projects that successfully implemented lean six sigma concepts?
As course instructors and student coaches we get a front-row view of the outstanding success the students achieve within their respective organizations. The results by these new practitioners demonstrate how easy it is to apply fundamental methods to achieve valuable results across a variety of industries. Here are a few examples:
-
A project for a major metropolitan city reduced the time needed to complete the purchase process for refuse vehicles by 52%, from 2.4 years to 1.3 years. The project utilized Lean principles to remove redundant steps, reduce the need for multiple approvals, and shortened the lead time related to key vehicle preparation activities. As a result, the city is able to more quickly replace the aging vehicles in their fleet.
-
An information technology project examined the way a large, educational organization imaged computers across three different support teams. The outcome was a savings of 4,311 labor hours per year, a reduction of $121,340 associated with labor and materials annually, providing the ability to shift staff resources to other critically needed value-added activities, and resulted in the three teams performing the work in a consistent and reliable manner for their customers.
-
An academic leader in higher education trained their team to use 5S techniques on their class website in order to keep materials organized and easy to find. In addition, the project identified faculty members who would be available to support each other if someone were unable to teach a class. Communication increased between faculty members to ensure courses and programs remain on track throughout each semester, and connected them with a support team to aid faculty in keeping up with their workloads. The result was an improvement in student satisfaction by 13% over previous years’ mean scores, and reduced negative ratings (defects) to 0%.
-
A food producer was able to achieve savings of approximately $9,000 per month by reducing the percentage of overweight granola bar products being made for one of their major customers. While overages were a benefit for the customer, it represented a significant cost to the producer. The producer was able to decrease the percentage of overweight products by 70.8%, and reduced variation in weight by 60.2%. As a result, the granola bars produced for their customer are now more consistent.
-
A manufacturer needed to reduce the changeover time between products being produced on a single production line. They needed to make 5-10 changeovers per month on the line. Initially, changeover times were lengthy and inconsistent, and the process also created excessive waste during the changeover process. In the first month, the changeover time decreased by 33%, and another 12% the following month, with continued improvements expected over time. As a result, the process became more consistent and variability in the changeover time decreased by 58%, producing a cost savings of approximately $695 per changeover.
All of these practitioners used fundamental improvement tools to make powerful impacts to their processes and achieve financial, time, and quality benefits for their organizations, as well as deliver improved service and products to their customers.
There is no need to be concerned by the thought of complicated tools or statistical analysis techniques. Lean Six Sigma is a methodology and tool set that is very accessible and usable by anyone, regardless of their role or the department in which they work in an organization.
For more information regarding the Lean Six Sigma and Six Sigma certifications offered by ASU’s Office of Global Outreach and Extended Education, please visit our website.
--
November 2020